About Polycarbonate
With an impact resistance 200x that of glass and at only half the weight, polycarbonate is an ideal substitute for glass in both internal and external applications.
What’s more, polycarbonate is an excellent safety glazing material, thanks to its impact and fire resistance, while still offering superlative levels of clarity.
Polycarbonate is therefore used in a wide variety of projects and applications where high clarity, but high-impact resistance is important. This includes everyday use such as sports eyewear equipment and machinery guards, as well as in construction uses such as shelters, canopies, greenhouses and nurseries.
About Acrylic
Like polycarbonate, acrylic is a clear plastic with outstanding impact resilience that still offers excellent clarity.
Acrylic has exceptionally high UV resistance, which makes it a perfect alternative to glass windows where strength is key, such as on aeroplanes. This quality also makes it ideal for outside signage, where constant UV exposure can quickly damage the print underneath.
In addition, acrylic’s lightweight, but strong properties make it ideal in a wide variety of applications such as security barriers, LCD screens, partition screening, even artificial fingernails.
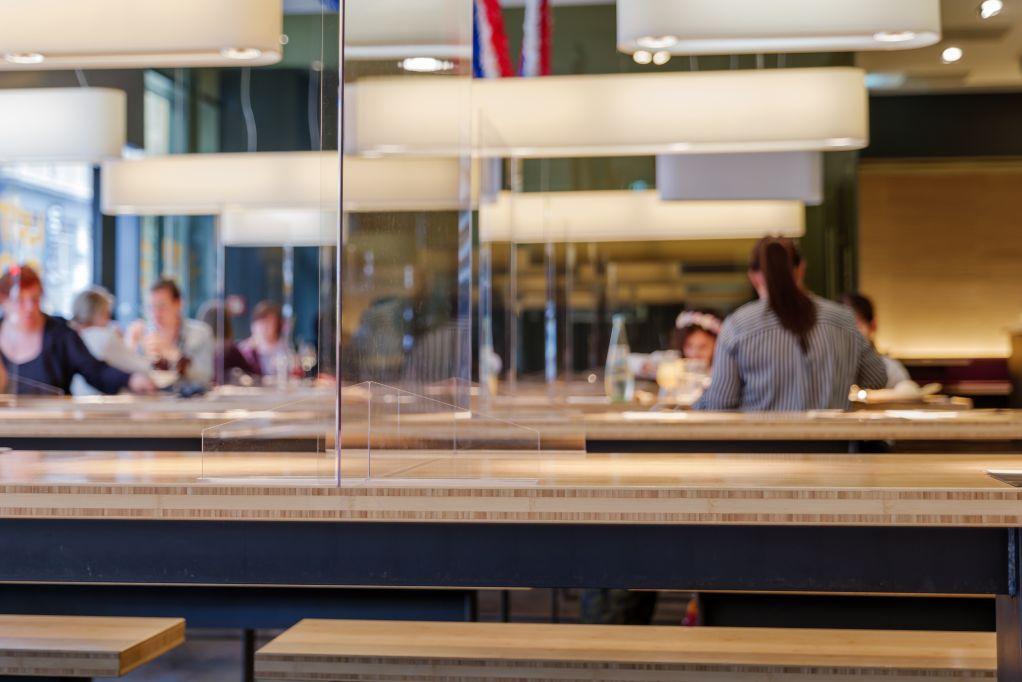
What Are The Differences Between Polycarbonate and Acrylic?
Both acrylic and polycarbonate are incredibly versatile and used in a variety of diverse applications. With the two products being very similar, we’re often asked which is the better material.
The fact is, it is highly dependent on the specific application, as well as other key factors such as shaping and budget.
We’ve detailed below some core strengths of the respective materials:
Strength
Acrylic is an impressive 17 times stronger than glass, but polycarbonate is the clear winner, with an average 200x the impact resistance of glass. For this reason, polycarbonate is regularly used as an alternative to glass in construction projects, as well as in uses where incredible shatter resistance is key, such as safety barriers, riot shields, glasses and goggles.
For uses where strength is paramount, our Abrasion Resistant Polycarbonate offers superior toughness - in short, it’s virtually unbreakable!
Weight
Given their varying difference in strength, you would expect that there might be a consequential effect in terms of weight. However, acrylic and polycarbonate are incredibly similar in terms of weight - with both weighing less than half that of glass.
If we delve into specifics, Acrylic is the technical winner, weighing in at 1.19 grams per cubic centimetre, compared to Polycarbonate which weighs 1.2 grams.
This almost negligible weight difference though means that focus can be applied in other respective key attributes.
Light and Clarity
When looking at an alternative to glass, optical transparency is one of the key deciding factors between acrylic and polycarbonate.
The good news is that they both offer fantastic transparency - for example (depending on thickness), our clear Cast Acrylic sheets offer 93% light transmission, while our Clear Polycarbonate offers similar exceptional light transmissions of between 80 - 92%.
For comparison, the light transmission of window glass is around 83-90%.
One key caveat though is that acrylic can be polished to restore clarity, whereas polycarbonate cannot.
UV Protection
Acrylic has very strong resilience to UV rays and similar weathering and some acrylics can even block up to 98% of UV rays.
Standard Polycarbonate doesn’t stand up to UV rays as well and can yellow slightly after being exposed for a long period of time.
Our Abrasion Resistant polycarbonates however are designed to withstand UV significantly better than ‘standard’ polycarbonates. In fact, our Longlife Polycarbonate Sheet features co-extruded eco protection on both sides of the sheet, which results in it cutting out 98% of harmful UV radiation. This makes it an ideal product in some of the world’s toughest climates.
The UV protective layer on both Abrasion Resistant and Longlife Polycarbonate enables longer sheet life expectancy, prevents yellowing and guards against loss of strength.
Heat and Chemical Resistance
Acrylic can be used in temperatures from as low as -35C to as high as 85C. Acrylic is prone to expansion and contraction when exposed to the elements, though only temporarily and will not change size permanently.
Polycarbonate however can withstand temperature much hotter - as high as around 130C - with the lowest working temperature around the same as acrylic. These properties also make it a superior material when it comes to chemical resistance, with polycarbonate being highly resistant to many acids and similar harsh chemicals.
Our Abrasion Resistant Polycarbonate goes a step further and includes an abrasion and chemical resistant coating, meaning superior protection against everyday scratches, targeted vandalism and other forms of physical attack.
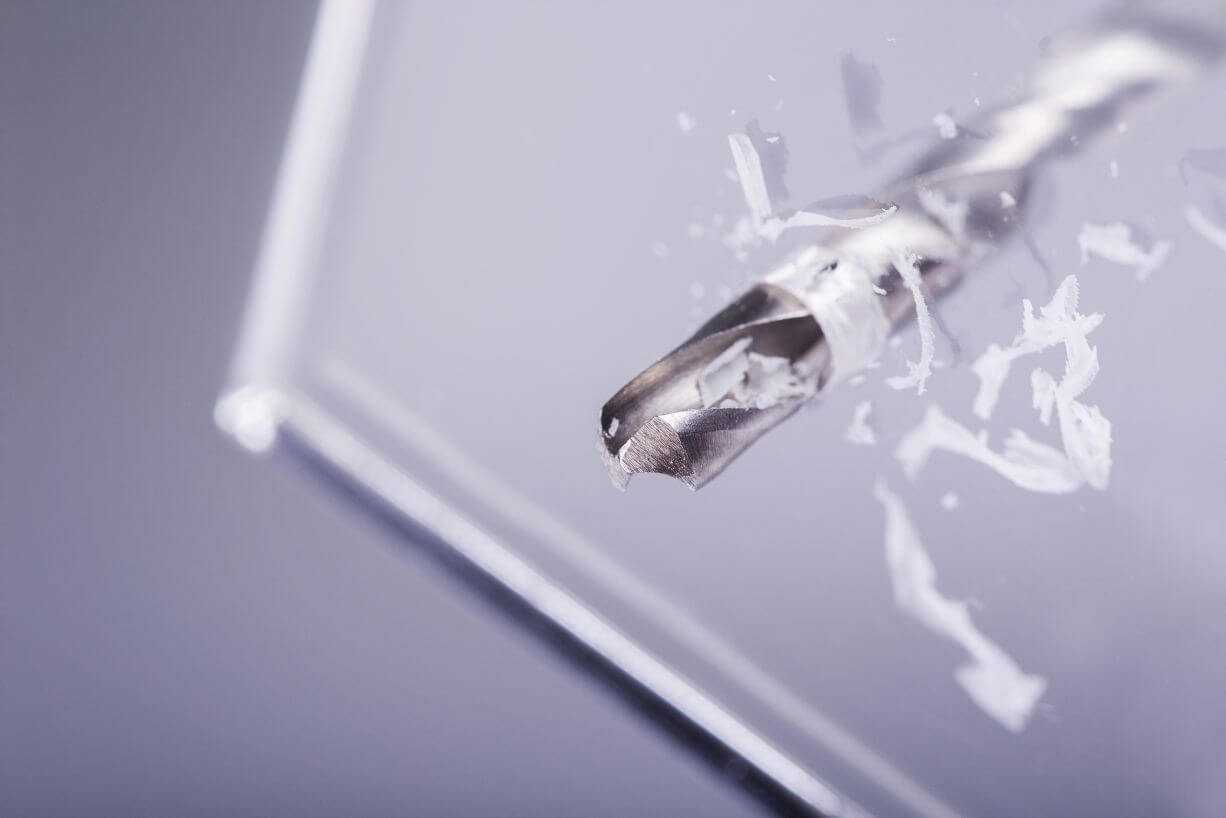
Machinability
One of the many benefits of acrylic and polycarbonate over a similar product like glass is its ability to be easily cut and bent, depending on the requirements.
Both materials can be cut using conventional cutting equipment, though polycarbonate’s superior strength does make it slightly harder to cut through and will offer some initial small resistance when cutting.
Polycarbonate’s strength once again plays in its favour when it comes to drilling, with acrylic being prone to cracking if not drilled carefully and with the right bits, especially at the edges. Polycarbonate on the other hand won’t crack when exposed to similar processes.
When it comes to bending, both are pretty flexible, though acrylic will require heat before being bent, while polycarbonate can be cold-formed.
Cleaning
As previously detailed, polycarbonate and acrylic’s clarity is what makes them a fantastic choice for when visibility is key. Of course, exposure to various elements, both indoor and out will mean regular cleaning to maintain optimal clarity.
Polycarbonate’s superior chemical resistance means that it can be cleaned using various chemical cleaning agents, whereas acrylic should only be cleaned with soapy water or special acrylic cleaner to avoid permanently marking the surface with chemicals.
As mentioned previously, Acrylic does have the upper hand when it comes to polishing - with acrylic being able to be polished to improve clarity.
Cost
Finally, we look at the cost of each material. Both offer excellent value for money, especially when compared to more expensive materials like glass. What’s more, their impressive strength and resilience mean less damage and more durability, ensuring they’ll last a lot longer than traditional materials.
Given its superior strength and resistance, polycarbonate tends to be the higher-priced material out of the two, with costs around a third more than the cheaper alternative, acrylic.
Need More Information?
We’ve only just touched the surface of the advantages and applications of both acrylic and polycarbonate. For a more detailed breakdown, including recommendations and advice from our expert team, contact your nearest Righton Blackburn Service Centre.
We cater to a broad range of trades, from the bespoke and intricate, to the demanding and large scale.
To discover the technical composition, characteristics, properties and applications of our incredibly vast product range, you can also visit our datasheet database.
Our Pledge
We only source materials from approved vendors and the most reputable mills, so all customers can trust in reliable, professional and high-quality manufacturing.