What is a sleeve bearing?
Also referred to as bushings, plain bearings or journal bearings, sleeve bearings are incredibly simple but highly effective components, containing a bearing surface and a mating component. Its role is to guarantee linear or rotational movement between two parts. Unlike the rolling action of a ball bearing or roller bearing, sleeve bearings have a sliding action and generally use self-lubrication to allow for smooth continuous operation. They provide a low coefficient of friction-reducing heat and providing substantial wear resistance. They are low cost and virtually maintenance-free, and as such used in many diverse applications.
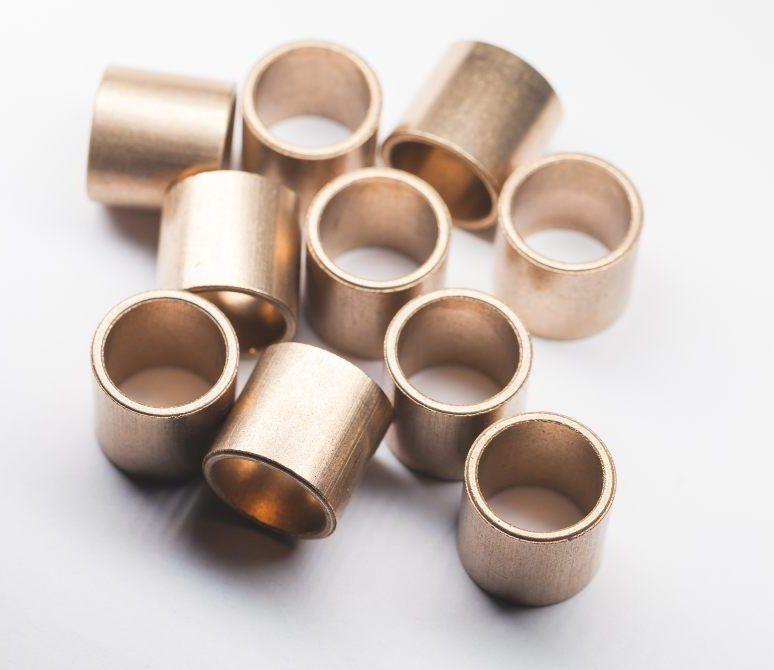
[Above: bronze sleeve bearings]
What does a sleeve bearing do?
Put simply, sleeve bearings safeguard optimal motion between two components, absorbing any friction and reducing potential vibrations. They are also ideal for heavy-duty projects due to significant allowability for load capacity.
The more robust sleeve bearings can cope with high loads and challenging temperatures and are also incredibly low wear.
Furthermore, they are capable of high shock load resistance due to a greater contact zone.
Sleeve bearings with a conformal liner can compensate for misalignment and dampen vibrations. This specialist bearing allows for low friction, and with a thinner wall section that requires less space to be housed.
Sleeve bearings are compact, easy to install and lightweight, and cater to a host of applications including transmission shafts, lift and tilt devices, electric motors, and clevis joints for hydraulic cylinder pins, and a great deal more besides.
Sleeve bearing design
The more common types of sleeve bearing are:
- Flanged bearing:designed for axial and side loads.
- Cylindrical bearing: for radial loads, and for higher side loads, a combination of both a thrust washer and a cylindrical bearing is often used.
Sleeve bearings are commonly made from bronze, steel or stainless steel, while brass and plastic sleeve bearings are also manufactured for specific applications.
Another sleeve material that may be used for lighter applications, is oil-impregnated bronze sleeve bearings. These bearings contain specific pores that absorb oil, which is then released under applied force and absorbed back into the bearing once the force dissipates.
In instances where constant lubrication is paramount, bronze sleeve bearings are the go-to product, these will sometimes utilize lubricant plugs (PTFE or graphite) to assist with any lubrication problems.
Choosing Bronze: The Value of Good Bearing Design
Having a well-designed bearing is of course paramount to its ongoing performance. Three key cornerstones unite these elements of good design:
- we must understand the service environment the bearing is to operate in
- an appreciation of the lubricating method is essential
- selecting an appropriate material for the job is paramount
Service Environment
The most important element when considering bearing performance is knowing where and how the bearing will be used.
Many factors must be taken into consideration in order to make an accurate assessment of this environment, including:
- What is the speed of the design load?
- Will the load oscillate?
- Is there a corrosive environment?
- What temperatures are in play?
- Is the load steady or impact?
- Will there be frequent start-stop operation?
- Is the environment dirty?
- Will lubricants be a factor?
- Is there shaft or journal bearing misalignment?
- Is there a hardness differential? Bearing vs shaft.
Lubrication Mode
Knowing the lubrication mode in which the bearing will operate is equally essential. Sometimes the mode can be identified through design, other times it is indicated by the operating conditions.
Material
Once the service conditions and lubrication method are in place, bearing material is selected to suit both the service environment and the operating mode.
The vast array of properties offered by the bearing bronzes ensures an easy selection process and ensures that the alloy chosen will provide suitable bearing performance.
Often, operating conditions have conflicting demands, and this makes almost every bearing design something of a compromise.
Conditions such as extremes of load, speed or temperature, when combined, can be especially challenging.
The bearing designer's job is then to ‘optimise the compromise’ - to bring out the highest possible performance in the finished bearing.
Defining the mode of operation
Once the operating conditions are established, we then need to define the lubrication mode.
This may be:
- Hydrodynamic Mode
- Boundary Lubrication Mode; or
- Mixed Film Mode
This can sometimes be done as part of the design specifics, but if not possible then it is defined by default.
Hydrodynamic Mode
This mode offers the lowest friction and lesser wear and is either called hydrodynamic or full-film operation.
The bearing becomes completely separated from the shaft (otherwise known as a 'Journal') by a continuous film of oil in the space between shaft and bearing.
The oil is placed under hydrodynamic force created by the relative motion between bearing and journal.
The appropriate Hydrodynamic conditions are inferred by the following factors:
- Velocity in excess of 25 surface feet per minute,
- Correct lubricant viscosity (higher viscosity increases load-carrying capacity, lower viscosity decreases the frictional coefficient)
- Does not oscillate
- Continuous lubricant flow
As the bearing and journal are not in contact in the hydrodynamic mode, frictional coefficients can be as low as 0.001. This is the same level as a high-precision ball style bearing and is markedly better than that encountered with roller bearings.
Furthermore, as there is no metal-to-metal friction there is also no wear and bearing life should be indefinite.
From a theoretical standpoint, the only significant material property requirement for hydrodnyamic bearings is that the bearing alloy must be strong enough to support the applied load.
At start-up, (or shut-down) however, there isn't the required velocity to establish full-film operation straight away. This means the bearing initially operates beyond the hydrodynamic scope, and just for a brief moment, there may be actual metal-on-metal contact.
This can also result if there are sudden changes in load or lubricant viscosity.
Having said that, hydrodynamic bearings are robust and can normally sustain these changes in load or shock loads up to ten times the design load for small amounts of time.
Boundary Lubrication Mode
Ordinarily, the most challenging conditions for bearings are when bearing and shaft actually touch or are only separated by the tiniest film of oil.
This is known as the ‘Boundary-film’ mode of operation.
The right elements for Boundary-film conditions are when:
- The bearing is grease-lubricated
- The bearings are lubricated periodically, as in hand oiling or greasing
- Reciprocated motion, or oscillation
- When the surface velocity is less than 10 surface feet per minute
Bearings that operate under boundary environments demand extreme care in material selection.
The bearing alloy selected must have low inherent friction, and must also resist welding and seizing. It will also have high thermal conductivity performance to remove frictional heat from the surface of the bearing.

[Above: sleeve bearing with lubrication holes]
Mixed Film Mode
Between hydrodynamic and boundary film mode lies a condition known as ‘Mixed-film mode’.
This exists when a part of the bearing’s surface is supported by a hydrodynamic oil film while the rest of the bearing operates with metal-to-metal ‘Boundary-film’ contact.
Mixed Film MNode is probably the most common of the three operating modes.
Bearing Bronze Material Properties
Bearings often operate suitably in the boundary and mixed-film modes for their entire service lives.
The only drawback for this is an increase in friction compared to hydrodynamically lubricated bearings and a resultant higher expenditure of energy.
Bearing life therefore relies heavily on the choice of bearing material.
Even hydrodynamic bearings will go through Boundary and Mixed-Film modes at start-up and shut down, or when faced with transient conditions.
This means that material selection is a pivotal design factor for all sleeve bearings, no matter what the operating mode.
General attributes of a good choice bearing material are:
- A low coefficient of friction when measured alongside hard shaft materials
- Good scoring resistance when measured against steel journals
- The ability to absorb and remove tiny contaminants
- The ability to adjust to the shaft roughness and misalignment
- High compressive strength
- High fatigue resistance
- Corrosion resistance
- Low shear strength at the bearing-to shaft interface
- Structural uniformity
A material’s frictional properties are most tested during those brief moments that a bearing operates in boundary mode.
Bearing cleanliness is of course paramount, but some degree of contamination is almost unavoidable.
A good bearing material, therefore, should be able to embed small dirt particles in its structure, keeping them distanced from the steel shaft, which might otherwise be affected.
There is also the danger that shafts can be misaligned, or not exactly smooth. A bearing alloy may therefore be called upon to wear in slightly to allow for any discrepancy. This process is called conformability and is related to the material’s hardness and compressive yield strength.
High yield strength also creates good fatigue resistance and together these are reliable predictors of a material's load-carrying capacity.
Good corrosion resistance is pivotal for projects in more challenging environments, increasing service duration and performance life.
A bearing material should also be structurally uniform, to ensure that its properties do not change as surface layers begin to wear.
Bronze sleeve bearings, therefore, offer a broad range of ductility, strength, wear resistance, hardness, anti-seizing and low friction properties, as well as the ability to adjust to discrepancies, tolerate dirty operating environments and allow for contaminated lubricants.
No bearing metals have greater machinability than the leaded and high-leaded bearing bronzes.
Bearing bronzes are an adaptable and broad-ranging family, whatever the required application, no matter how demanding the environment, there will be a bearing bronze that can be applied.
The Bearing Bronze Family
We have listed some of the more common bearing bronzes and their distinct alloy families.
Tin Bronze Alloys: C90300, C90500, C90700 | Being strong and hard and having very high ductility, tin bronzes have high load-carrying capability, as well as good wear resistance and an ability to withstand pounding. These alloys are further noted for their corrosion resistance in seawater and brines. |
Leaded Tin Bronze Alloys: C92200, C92300, C92700 | The main utility of lead is to improve machinability, but it is only used in small concentrations to not affect the material properties in any adverse way. A few of the leaded bronzes also contain zinc, strengthening the alloys at a lesser cost than tin. |
High-Leaded Tin Bronze Alloys: C93200, C93400, C93500, C93700, C93800, C94300 | In this bronze family, strength and hardness are found to be markedly less than presented in the tin bronzes, but this group of leaded alloys excel in both antifriction and machining attributes. |
Aluminium Bronze: Alloys: C95300, C95300-HT, C95400, C95400-HT, C95500, C95500-HT, C95510 | Aluminium bronzes are the strongest of copper-based bearing alloys. They also show superior strength at elevated temperatures and are the only bearing bronzes capable of being heat-treated. |
Manganese Bronze Alloys: C86300, C86400 | Manganese bronzes unite very high strength with substantial corrosion resistance. Manganese bronze bearings also perform well at high speeds under heavy loads, but they do require high shaft hardness and non-abrasive operating conditions. |
Righton Blackburns Sleeve Bearings
Here at Righton Blackburns, we stock a substantial range of bronze and steel sleeve bearings.
We are also the sole UK distributor of Hardiall® - a high hardness and low friction copper alloy designed for extreme conditions, manufactured by Lebronze alloys.
Hardiall’s use in brushing and bearings (among other forms) is increasingly being used in a wide range of industries where thanks to the unique combination of properties it is helping to prevent failures and ensure a longer lifespan compared to traditional materials. Industries include motorsport, aerospace, oil & gas, construction, mining & heavy transport, automotive, defence, space, marine, power transmission and renewable energy.