Righton Blackburns offers pre-anodised aluminium sheet page and sublimation aluminium. For more information, contact your local service centre.
1. Mechanical Finishing Methods
The first collection are finishes created by mechanical processes. Aluminium can be buffed, sanded, ground or blasted and all the following methods are used to improve surface presentation or ready the material for other cosmetic enhancements.
Grinding
Grinding produces a surface finish that is extremely flat and blemish-free. To do this, a rotating abrasive wheel is used to remove anomalous surface material. A potential drawback to this method is that the machinery can get clogged with aluminium shards, but there are measures available to combat this likelihood.
If grinding is the chosen path, then the preferred method is to grind at a slow speed using aluminium oxide to prevent the surface from overheating.
Abrasive Blasting
This method can be utilised in two contrasting ways, to either roughen a smooth surface or smooth out a rough one, it is also often the selected method to remove surface contamination debris or for more finite shaping. To do this, pressurised fluid is used to ‘blast’ the surface with various optional materials, which may include glass beads, baking soda, metal shot and sand to name a few.
Mass Finishing
Mass finishing methods are used to smooth and polish rough surfaces, a typical example would be tumbling. To tumble metal, parts are placed into a barrel with a chosen media, then rotated for a specified period of time to buff and shape the metal through contact.
Polishing
This method employs a profile polishing machine to create a startling specular reflective surface. The process uses a soft cloth charged with abrasive grains which then wipe across the surface of the metal bringing out the shine.
Buffing
Buffing wheels are usually made by sewing muslin discs together. The process itself is similar to polishing but uses less abrasive grains and is traditionally used to remove emery marks.
2. Anodising Finishing Method
Anodising is an electrochemical process that creates added protection to aluminium’s natural oxide film.
This process is utilised after extrusion through the submerging of the aluminium component in an electrolytic bath. Once immersed, a high amperage but low voltage current is fed into the bath, and an oxidation reaction takes place as the current flows through the aluminium, creating a thicker layer of oxide. This tough, porous, anodic oxide layer results in a firm, very durable, and inert outer film creating a metal with exceptional abrasion resistance, better heat dissipation and better corrosion resistance than its non-anodised counterparts.
Another huge plus with anodised aluminium is that it can be readily coloured, and any kind of anodised aluminium alloy can be used.
Why is anodised aluminium so easy to colour?
During the anodising process, the surface of aluminium becomes porous, the resultant micropores are ideal for dye application, acting as pools in which the dye can collect.
Once the dye is applied, these ‘pools’ are sealed and the colour becomes embedded within the oxide layer. This results in the dye being an integral part of the layer itself, providing much greater resistance to peeling or fading.
The thickness of anodic film advisable will depend largely on the environment, but usually, you should aim for tolerances of between 5 and 25 microns. As the environment becomes more demanding, so thicker films should be applied.
In the commercial world, anodising is mostly found where colour and design are prerequisites, but corrosion resistance is also a dominant factor.
Anodised aluminium is excellent for applications where aesthetics, durability and distinctive interior décor is required. Not just limited to interior design though, anodised aluminium provides excellent opportunities for cladding, roof finishes and trims and has been used widely in both commercial and domestic architectural and design applications throughout the world. Sports equipment, the car industry and handheld devices we use every day such as phone cases and tablets often contain anodised aluminium.
Righton Blackburns have available from stock, a wide range of pre-anodised aluminium in colours and finishes from bright to special finishes, including patterned and coloured anodised coil. We can supply material slit and cut to length to bespoke sizes specified by the customer. Find out more on our pre-anodised aluminium.
3. Bright Dip Anodising
This method involves two back-to-back processes:
The first of these is bright dipping, a process of bathing the extrusion in a phosphoric and nitric acid solution. The dual purpose of this is to smooth any surface peaks and troughs as well as creating a shiny specular or ‘mirror’ finish,
This is then followed by the aforementioned anodising process, which enhances corrosion protection.
Bright dip anodising lends itself much more to some extrusion profiles than others, commonly found bright dipped shapes would be tubes, angles and channels with tubing being the most prevalent of these.
Bright dipped tubing is often used for architectural enhancements such as railing or trim, whereas channels and angles are used to secure fixed glass panels or mirror installations fixed to walls or custom shelving.
But when it comes to bright dipping, all alloys are not created equal. Structural aluminium (aluminiums 6061 and 6063) are actually not good choices for bright dipping. They still have some aesthetic quality but lack the brightness and “wow factor” bright dipping is intended to create.
Make way for aluminium 6463 - a variant of 6063 that holds its shine much better and is an ideal candidate for bright dip anodising.
Is bright dip anodising safe?
In inexperienced hands, no is the simple answer.
Phosphoric acid and nitric acid are toxic to humans. The bright dipping process creates Nitric oxide and Nitrogen dioxide, known commonly as NOx. These chemicals must be very closely monitored by experienced technicians and specific safety measures MUST be in place to limit and control the resultant gases.
So as an option, bright dipping can provide a superb shine and rigid resistance against the elements, but you must search for an experienced manufacturer who understands how to manage its dangers and drawbacks.
All in all, anodising is a fantastic solution for the right type of products, but many variables do need to be taken into account though before deciding on the anodising route.
Bath type, temperature, voltage and amperage all need to be evaluated in order to produce consistent, high quality results. Anodising can also slightly increase the overall dimensions of extrusion so isn't recommended if dealing with extremely tight size tolerances.
As with any unfamiliar process we would always advise speaking to an expert who can explain the advantages and pitfalls of these processes, and indeed suggest relevant alternatives where more appropriate.
In general though, if you require the simple characteristics of corrosion resistance and a stunning metallic shine, or you need a product with improved emissivity or substantial adherence to glue or primers, then anodising can be the perfect solution. If, however, electrical conductivity is a must, or additional forming processes are needed, then anodising would not be our recommended route.
4. Powder Coating
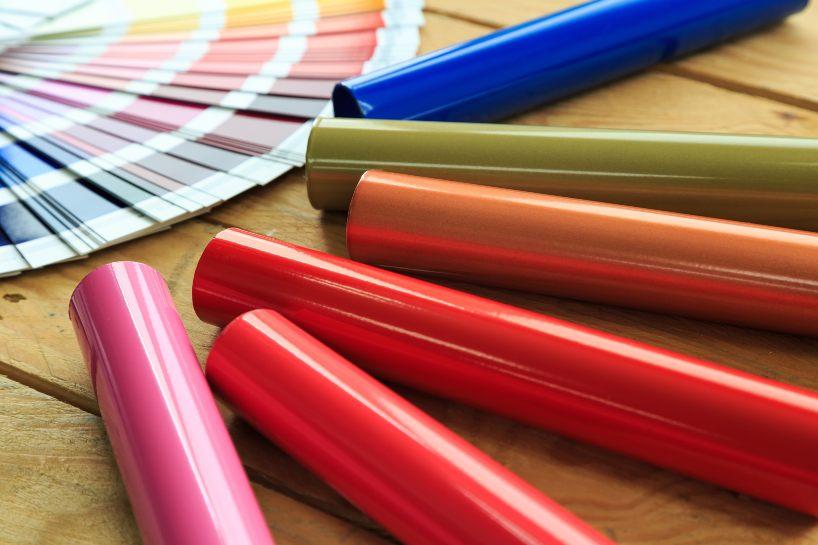
This is a process where electrostatically-charged paint (in powder form) is sprayed onto the extrusion, but unlike liquid paint, powder coating doesn’t require a solvent to create adhesion.
Pre-treatment is a very important step in powder coating, ensuring that the surface to be painted is smooth and readily accepts the natural adhesion within the paint.
Once all the dust, grime and all other extraneous foreign particles have been removed the paint should remain ‘stuck’ and flake-free.
Next, the ‘powder’ is loaded into an electrostatic spray gun.
Once spraying commences, it is subjected to a positive charge, meaning that the powder bonds effectively with the electrically grounded extrusion.
The next step is to heat the aluminium profiles in a curing oven, where the coating is melted onto the extrusion surface in an even and smooth distribution.
After the baking step, a technician will remove them to cool and this allows the surface to harden.
Powder Coating Benefits
The principal benefits of powder coating are its wide assortment of colour options and its bright, impactful appearance.
Coating this way is also durable, thick and unlikely to chip or peel easily.
Since this method does not use solvents or VOCs (Volatile Organic Compounds) there is no environmental damage caused during spraying, and any waste powder can be collected up and re-used for another job.
Admittedly you may not get the same punch of colour that anodising may provide but the colour range is almost limitless and when coupled with sublimation it is even possible to create aluminium that looks alot like wood!
In summary, unless there is a specific reason for choosing another finishing option, powder coating has a range of benefits and very few drawbacks, place this alongside its minimal environmental impact and powder coating is definitely a sound and safe choice.
5. Sublimation
For many in the architectural and interior design sectors, sublimation products are a relatively new concept, although sublimation printing is a familiar term within the printing industry.
Sublimation is a method of transferring full-colour graphics or photographs onto a wide selection of products, including metals, ceramics and unisub plastics and glass items - all specially pre-coated and therefore sublimation receptive.
For aluminium sublimation, a coloured or decorative film is wrapped around the extrusion and air is removed from the space between the film and the aluminium. After the wrapping stage, the extrusion is placed back into a curing oven and as it heats, the wood grain pattern is imprinted from the film to the aluminium. Extrusions are removed from the oven, and the film itself is taken away. At this point the imprint will be fully transferred onto the aluminium profile for the finished look, it is then allowed to cool.
Righton Blackburns is the leading supplier of sublimation aluminium in the UK and many worldwide markets. We believe the opportunities for aluminium sublimation offer an innovative opportunity to apply custom designs and photographs onto aluminium panels for uses such as interior décor. Find out more about our aluminium sublimation printing services.
6. Liquid Paint Coating
Once again, we would advise pre-treating the surface to ensure a smooth and flake-free finish.
Liquid painting of aluminium is still extremely common these days, easier than other methods and providing huge variety in both colour and composition variants, liquid paint is very much the go-to aluminium finish.
While there are numerous benefits to this method, there are also potential drawbacks and environmental considerations that must be recognised.
Firstly, liquid coatings create more waste than powder and consistent colour can be difficult to achieve using this method.
Also, liquid coatings will generally contain VOCs (Volatile Organic Compounds). These are often removed during any curing processes that the extrusion may undergo, but still present very real health concerns.
In essence, where VOCs are present they are definitely harmful to humans and the environment, akin to that of car exhaust fumes.
This danger can be limited but requires the use of expensive VOC abatement equipment. It is always advisable to seek expert advice before choosing Liquid Paint as a method and to check whether your chosen manufacturer has an on-site VOC abatement system.
If these essential steps are correctly addressed, then Liquid Painting can be ideal and is predominantly used for small batch production due to its colour inconsistencies.
One substantial advantage that liquid painting does have is its variety, paint types such as acrylics, silicone, polyester and PVDF (polyvinylidene fluoride) can all be painted.
Coating with PVDF
Polyvinyl fluoride (PVDF) is a thermoplastic fluoropolymer that incorporates a number of benefits, it is chemically resistant and non-reactive as well as being lightweight and having minimal thermal conductivity.
A primary advantage is that it is unaffected by most chemicals and solvents at the same time as being highly wear and abrasion-resistant.
A final standout point is that it can self-extinguish, thereby minimising smoke dispersal in the event of a fire.
For all of these reasons, it is an excellent choice in the areas of chemical processing and other chemically driven environments.
As with all methods of finishing there are plus points, but also negatives that should be weighed, in the case of PVDF the processing machinery needs to be meticulously clean, it also has a high dissipation factor and poor resistance to fuming acids.
Comparing Liquid Paint With Other Finishes
When placed directly side by side with powder coating, liquid painting will provide slightly more colour options but does produce harmful VOCs and is slightly more vulnerable to chipping, so it is the consumers job to weigh up these pros and cons.
Making the same comparison with anodising and dyeing and liquid paint is a clear winner when it comes to colour options and brightness but does lack when seeking to attain that aluminium ‘shine’.
Anodising also retains its colour better when exposed to sunlight and other elements.
In summary, liquid painting is a very popular choice of finish, its huge range of colour options make it extremely accessible and an excellent choice for the right projects.
Environmentally, though it is superseded by powder coating and the two should be closely compared when considering the requirements of a given job. It also lacks colour consistency, so if this is a definitely prerequisite then you may wish to steer away from liquid painting as your finishing choice.
Summary
The right choice for your own project comes down to many criteria - budget, machinery availability, and what the end goal is are all primary factors as well as safety measures and working environment.
To save you time and costs, Righton Blackburns offers pre-painted, pre-anodised, bright rolled finishes, and polycoating (to protect surface finish). A sheet suitable for sublimation printing is also available. Find out more about our processing and facilities.
Our special finishes are widely used in the lighting, trophy, engraving, sign and architectural markets.
Expert advice is only a call away, so if you have any concerns or just need to know a little more about your options please contact your local service centre.